Supply Chain Exception Management: Benefits of Same-Day Delivery Logistics
July 22, 2024
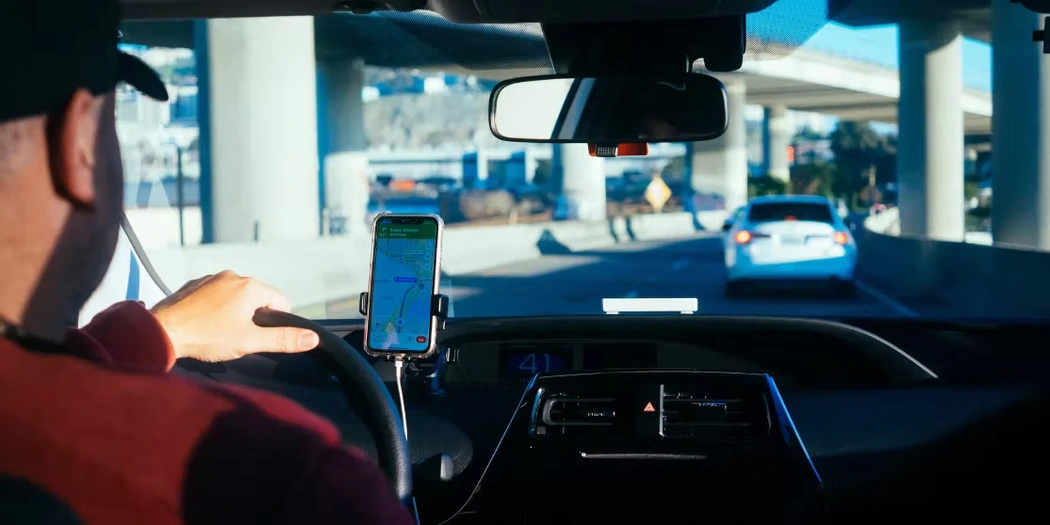
Who doesn't face challenges in the supply chain these days? Whether it's a delayed shipment or a sudden change in demand, these hiccups can throw everything off balance. The question is, how do you handle them without causing more chaos? That’s where supply chain exception management comes into play.
In this article, we will discuss best practices for managing supply chain exceptions. These tips will help you deal with the unexpected with confidence no matter what comes your way.
What is Supply Chain Exception Management?
Supply chain exception management is the process of dealing with unexpected problems that can disrupt the smooth flow of materials. For companies moving building materials, these disruptions are inconvenient and can be costly.
Imagine having a construction site waiting on a crucial delivery, only to find out it’s delayed or missing altogether. The ripple effect can slow down projects, increase costs, and damage client relationships.
Without a system in place to handle these hiccups, your business risks falling behind. Here are some reasons why exceptions occur:
- Manually Tracking Everything: Relying on manual processes is a recipe for disaster. It’s time-consuming, prone to errors, and leaves you blind to potential issues until it’s too late.
- Scalability Issues: As your business grows, so do the complexities of your supply chain. What worked when you were smaller won’t cut it anymore. Without a scalable solution, you’ll struggle to keep up.
- Communication Breakdowns: When there’s a breakdown—whether it’s between your team, suppliers, or drivers— it can cause major delays and mistakes.
How Curri Helps with Supply Chain Exception Management
Curri is a delivery service tailored specifically for companies that need building materials and equipment moved quickly and efficiently. With Curri’s same-day delivery option, you can respond to supply chain disruptions in real time. Instead of waiting days for a replacement part or urgent materials, Curri gets it to your site the same day. Best of all, supply chain exception management doesn’t have to be a manual headache. With same-day delivery logistics solutions, you can automate the entire process. Curri’s automated systems allow you to track packages and routes in real-time, so you always know where your materials are and when they’ll arrive.
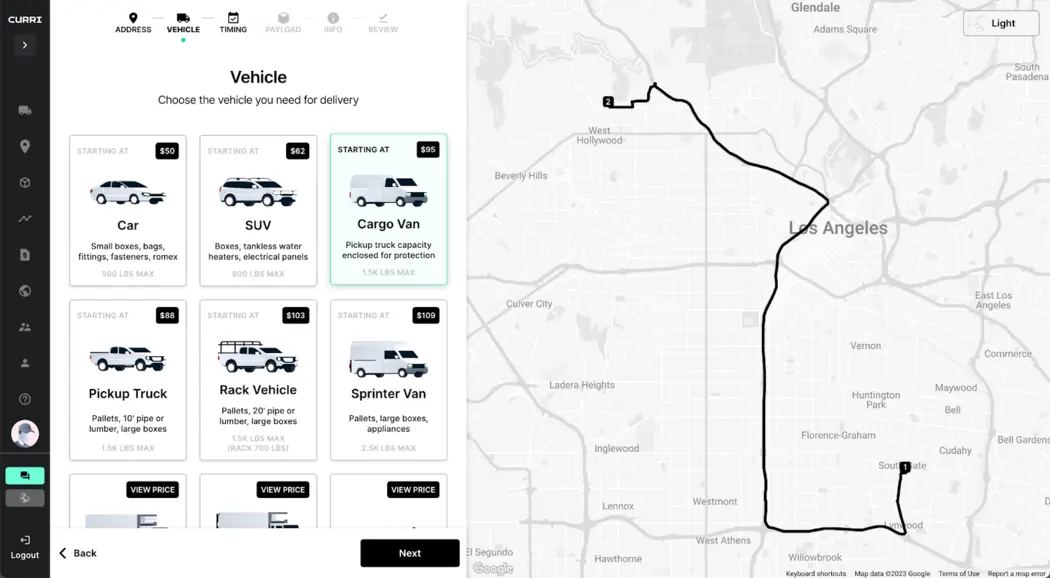
What Is a Delivery Exception?
A delivery exception occurs when an item or shipment does not arrive at its intended destination as expected. Exceptions can cause big headaches for distributors, who are dealing with a huge number of deliveries across multiple carriers every day.
The greatest challenge is that many exceptions go undetected until it's too late - when corrective action could have prevented bigger issues down the line. Often, the first sign of a problem is when a client calls to ask why their materials haven’t arrived. By then, the damage is done.
To avoid this, distributors need real-time visibility and tracking of each package. This allows them to be aware of any errors as soon as they happen and address them quickly before they snowball into larger problems.
Curri acts as your go-to partner for handling all your supply exceptions. We make sure your materials get delivered on time. We match you with drivers for your needs, balancing price, quality, and speed to fit your business perfectly.
Think of Curri as your GPS for construction materials. But instead of giving you directions, it keeps you updated on where your materials are at every moment. So, while Curri handles your deliveries, you can focus on what really matters—running your business with confidence. And that can only be done peacefully if you know everything’s on track.
Effects of Supply Chain Exceptions
Supply chain exceptions come with a lot of problems. When things go wrong, the ripple effects can be massive.
Increased Delivery Delays
When a supply chain exception occurs, delivery schedules get thrown off. This can lead to critical delays, slowing down your entire project and creating a backlog that’s tough to clear.
Higher Operational Costs
Dealing with exceptions often means extra costs. Whether it’s paying for expedited shipping or managing inventory adjustments, these issues can quickly add up and eat into your budget.
Customer Dissatisfaction
Late or missing deliveries frustrate your customers, leading to complaints and lost trust. When clients can’t rely on you to meet deadlines, they are less likely to work with you (which ultimately leads to lower revenue and fewer orders).
Reduced Supply Chain Visibility
Exceptions can cloud your view of the supply chain. It may seem like everything is on track - but everything is messed up in the background. Without clear, real-time information, it’s harder to track materials, manage resources, and respond to problems quickly.
Inventory Shortages
If exceptions aren’t managed properly, they can result in inventory shortages. This leaves your clients scrambling to find the materials they need, causing project delays and disruptions.
Decreased Supplier Reliability
Frequent exceptions can strain relationships with suppliers. If you can’t meet your expectations, they might need to rethink who you’re partnering with.
Lower Profit Margins
The additional costs and inefficiencies brought on by exceptions can squeeze your profit margins, making it harder to maintain a healthy bottom line.
Increased Return Rates
Poor handling of supply chain exceptions can lead to more product returns. Whether due to damaged goods or incorrect deliveries, higher return rates are a costly consequence.
Negative Brand Reputation
When exceptions aren’t managed well, it doesn’t just affect the current project—it can tarnish your brand’s reputation. Word spreads, and soon, potential clients might be reluctant to do business with you.
Thank you for reading this article. Please enjoy $40 off any Curri delivery by clicking on this link to sign-up.
Causes of Shipping Exceptions
There isn’t a single cause for shipping exceptions, which makes them difficult to predict and prevent. Various factors can come into play, each adding a layer of complexity to your supply chain.
First-mile delivery exceptions
Inaccurate Inventory Data
If your inventory counts are off, you might promise materials that aren’t available or delay orders because you didn’t know you were running low. It can create a domino effect of problems throughout the supply chain. That is why it needs to be solved first and foremost.
Delayed Order Processing
When orders aren’t processed quickly, everything slows down. Materials are not loaded on time, don’t get dispatched on time, nor delivered on time.
Packaging Errors
Incorrect or inadequate packaging can cause materials to get damaged in transit or make them difficult to handle. For companies dealing with heavy or fragile building materials like solar equipment, packaging errors can lead to returns, delays, and additional costs.
That’s why you need trained drivers who know how to handle your materials with care. With Curri, you get access to a quality driver network backed by up to $250,000 of coverage for every delivery you send.
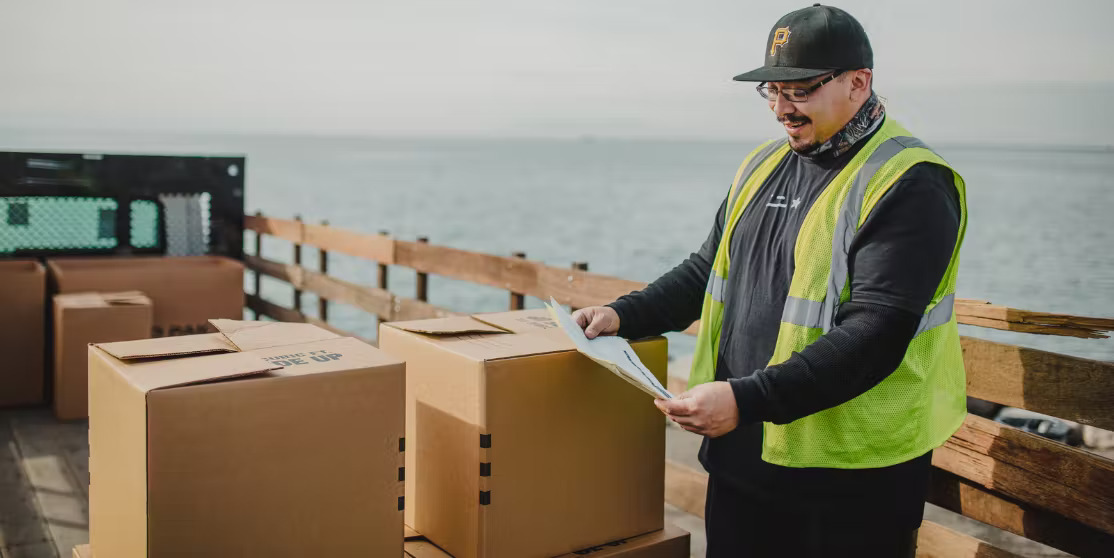
Supplier Delays
Even if you’re on top of your game, your suppliers might not be. If they experience delays, it directly impacts your ability to deliver materials on time. This can be frustrating and costly, especially when you’re relying on just-in-time delivery to keep projects moving.
Last-mile delivery exceptions
Incorrect Delivery Address
Sending materials to the wrong address can cause significant delays and confusion. Not only do you lose time correcting the mistake, but you also risk damaging relationships with clients who expect their materials on time and in the right place.
Traffic Delays
Traffic is unpredictable, and even the best-planned deliveries can be delayed by unexpected congestion. For construction companies, where materials often need to be delivered to sites in busy areas, this can cause serious disruptions.
But with Curri’s route planner, it’s easier to navigate around busy routes. Our technology helps find the quickest, most efficient paths for drivers, allowing you to avoid traffic and delays.
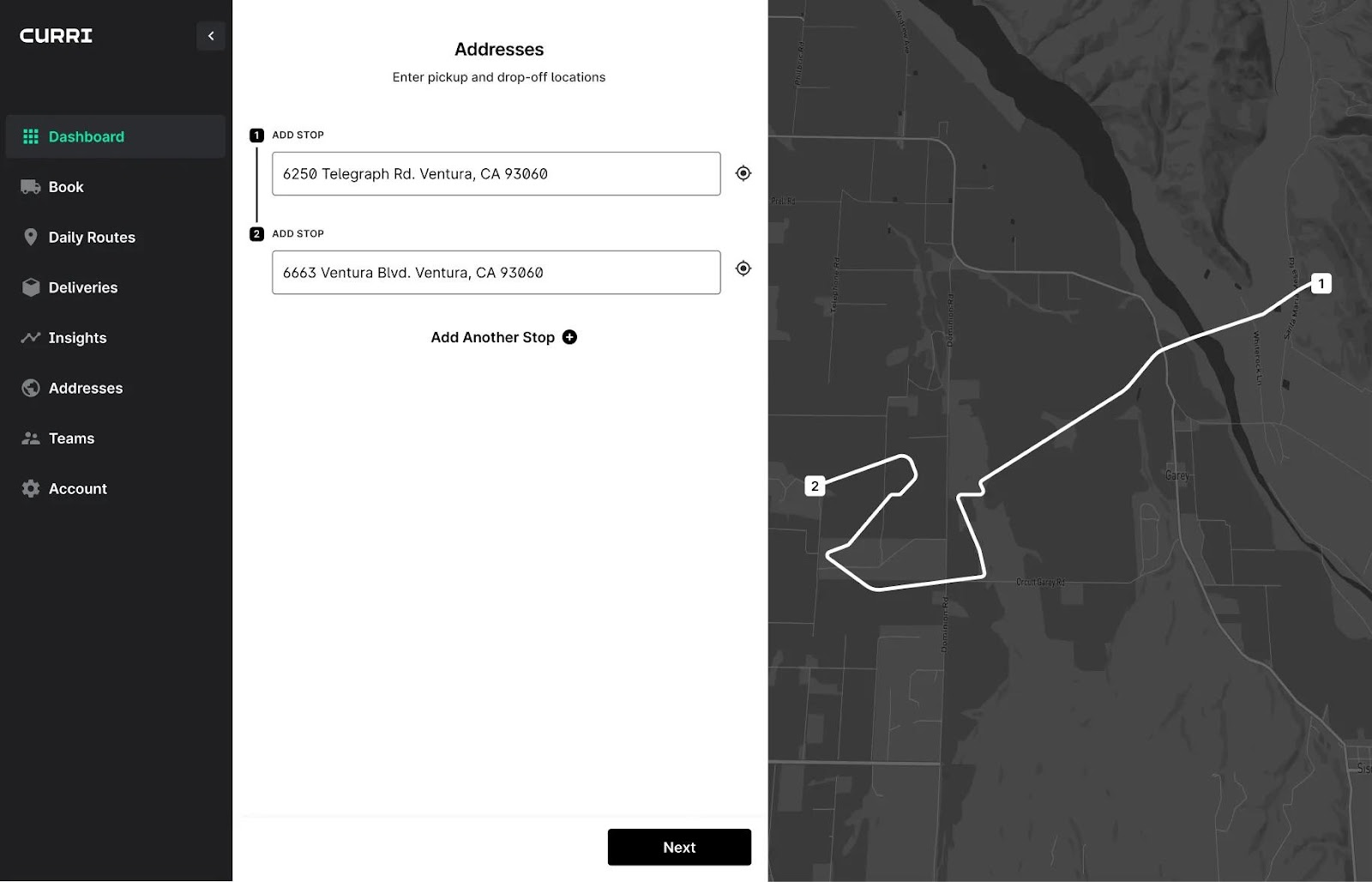
Weather Conditions
Weather is one of those factors that’s completely out of your control, but it can wreak havoc on your delivery schedule. From storms to heavy snow, bad weather can delay or even halt deliveries, leaving you scrambling to find solutions.
Delivery Vehicle Breakdowns
Another unexpected issue that can cause delays is a breakdown in the delivery vehicle. If the vehicle transporting your materials breaks down, it can lead to significant hold-ups, especially if the replacement vehicle isn’t readily available. That’s where a flexible on-demand delivery network like Curri helps. If a vehicle in your fleet breaks down, you can access drivers and vehicles from our nationwide fleet to fill the gap.
Thank you for reading this article. Please enjoy $40 off any Curri delivery by clicking on this link to sign-up.
How Exception Management in Logistics Works?
Exception management in logistics is all about identifying and addressing disruptions before they become bigger problems.
The first step is real-time visibility. Without it, you’re left reacting to issues after they’ve already caused delays or other headaches. With tools like Curri, you gain a clear view of your entire delivery process—from the moment materials leave the warehouse to when they arrive at the job site.
Next, you need a system in place to handle exceptions as they arise. This could mean rerouting deliveries, contacting suppliers for replacements, or even switching to a different delivery method if necessary. The key is to act fast.
Automation also plays a crucial role in effective exception management. By automating routine processes—like tracking shipments, updating delivery statuses, and alerting customers—you free up your team to focus on more critical tasks. Automation ensures that no detail is overlooked and everything is handled efficiently, reducing the chances of human error.
Benefits of Freight Exception Management
The biggest benefit of freight exception management? You avoid the nightmare of dealing with unexpected disruptions. Here are some more benefits of supply chain exception management:
Improved Customer Satisfaction
Your customers notice when you manage freight exceptions well. Delivering materials on time, even when unexpected issues arise, builds trust and reliability. Customers appreciate knowing that they can count on you to keep their projects on track, no matter what.
This leads to stronger relationships, repeat business, and positive word-of-mouth, all of which are invaluable to your growth.
Enhanced Delivery Accuracy
Freight exception management ensures that deliveries are handled with precision, even when things go off course. Accurate deliveries also mean fewer returns and corrections, saving time and resources. When you consistently hit the mark with your deliveries, you minimize the disruptions that can derail projects and cause frustration.
Reduced Operational Costs
Fixing issues before they grow keeps costs down. Things like expedited shipping or last-minute replacements can add up. But by being proactive, you avoid those extra expenses.
You also waste less when you handle exceptions well. Fewer rerouted deliveries, less damage, and fewer replacements mean lower costs. The more efficiently you manage things, the better it is for your bottom line.
Better Inventory Management
With real-time tracking, you always know where your materials are. This helps you manage stock levels better, avoiding both overstocking and shortages.
Better inventory management means fewer delays. When you know what you have and what’s on the way, you can plan better and manage supply chain exceptions effectively.
Strengthened Supplier Relationships
When suppliers see you’re on top of things, they’re more likely to prioritize your orders. A strong relationship means fewer disruptions and smoother operations. Everyone wins.
Increased Supply Chain Visibility
One big benefit of supply chain exception management is clear visibility. You know where every shipment is in real time. Better visibility also means faster responses to problems. Whether it’s rerouting a delivery or adjusting schedules, you stay in control.
Improve Supply Chain With Curri’s Exception Management Tools
With Curri’s exception management tools, the supply chain doesn’t have to be a constant headache. Curri gives you the power to handle it all without missing a beat. Here’s how:
Enhance Logistics with Integrated Same-Day Couriers
Imagine you’re trying to make 50 deliveries in a day, and suddenly, something goes wrong. Maybe a vehicle breaks down, or traffic comes to a standstill. Normally, this could throw your whole schedule off.
But with Curri’s integrated same-day couriers, you’ve got a backup plan. Curri steps in with the right vehicle, at the right time, to keep things moving.
So instead of scrambling to fix the problem, you can focus on making sure those 50 deliveries get where they need to go—on time and with no extra stress.
Optimize Routes for Construction and Industrial Supplies
When you’re delivering construction and industrial supplies, every minute counts. Traffic jams, unexpected weather, and road closures can all throw a wrench in your plans. That’s where Curri’s route optimization comes in. It helps you find the best possible path for each delivery.
Curri’s route planning tools take into account real-time traffic conditions, weather patterns, and even road restrictions to ensure your materials get where they need to be as quickly and efficiently as possible. In return, you save time and fuel and reduce the stress of managing multiple deliveries.
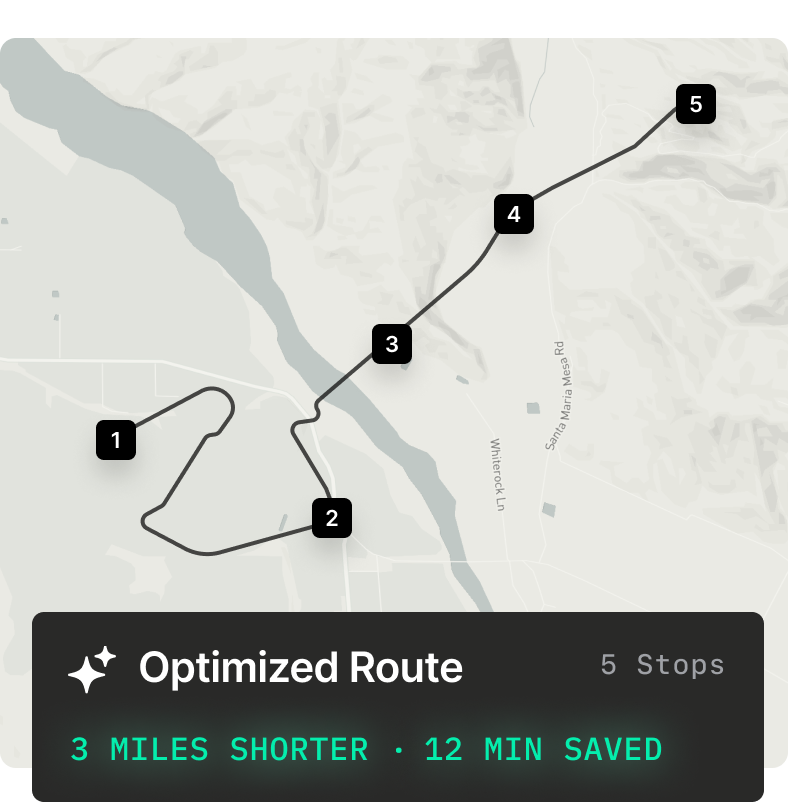
Achieve Fleet Elasticity
Even the best plans can face unexpected challenges. That’s why you need a flexible fleet that can handle anything thrown your way. Curri’s versatile fleet is built to manage any delivery, from small packages to large construction materials. Whether you’re dealing with a sudden spike in demand or an unexpected delay, Curri has you covered.
Curri provides fleet elasticity so that you only pay for what you need — freeing up money that would otherwise be used on fuel, maintenance, and staffing costs.
With Curri at your side, you can offer your customers on-demand supply delivery. No more worrying about not having the right vehicle for the job.
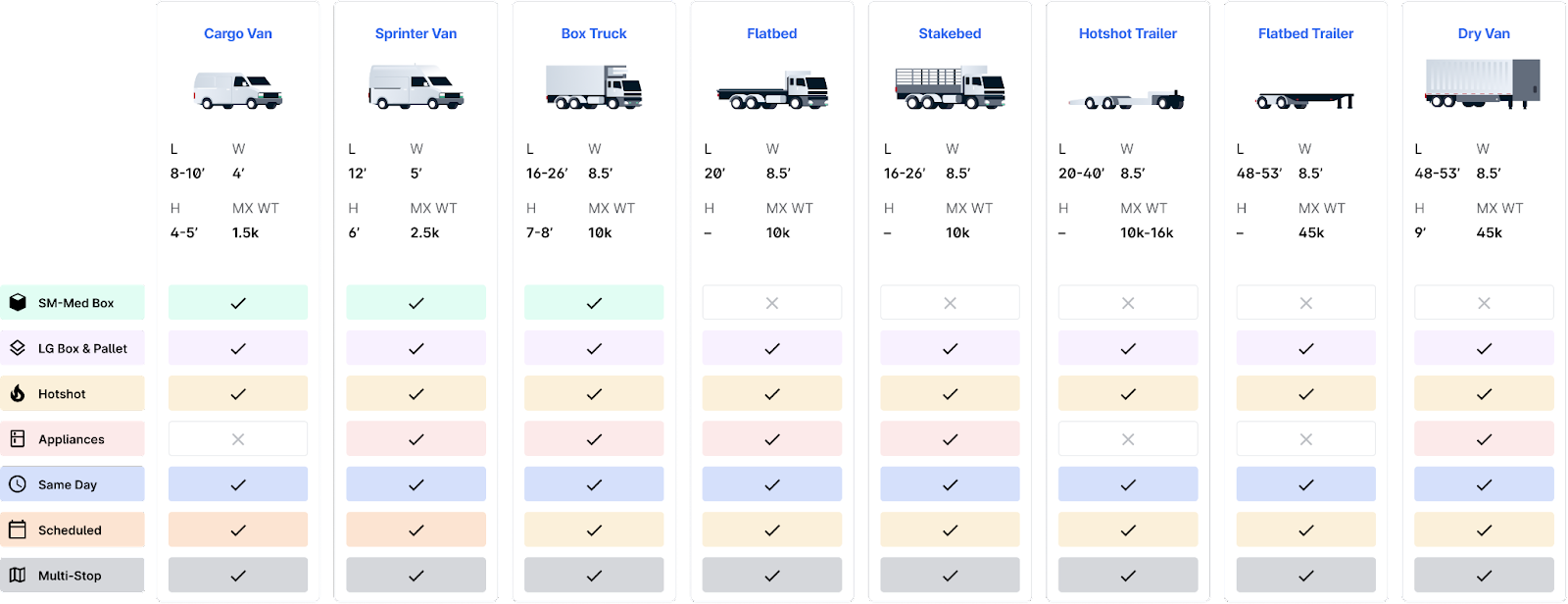
Enhance Visibility with Live Tracking and Notifications
Curri’s live tracking and notifications help you know where your deliveries are at any given moment. You can see your deliveries in real-time, tracking their progress and ensuring everything is on schedule.
With live updates, you’re always in the loop. If something changes—a delay, a reroute, anything—you’ll know right away.
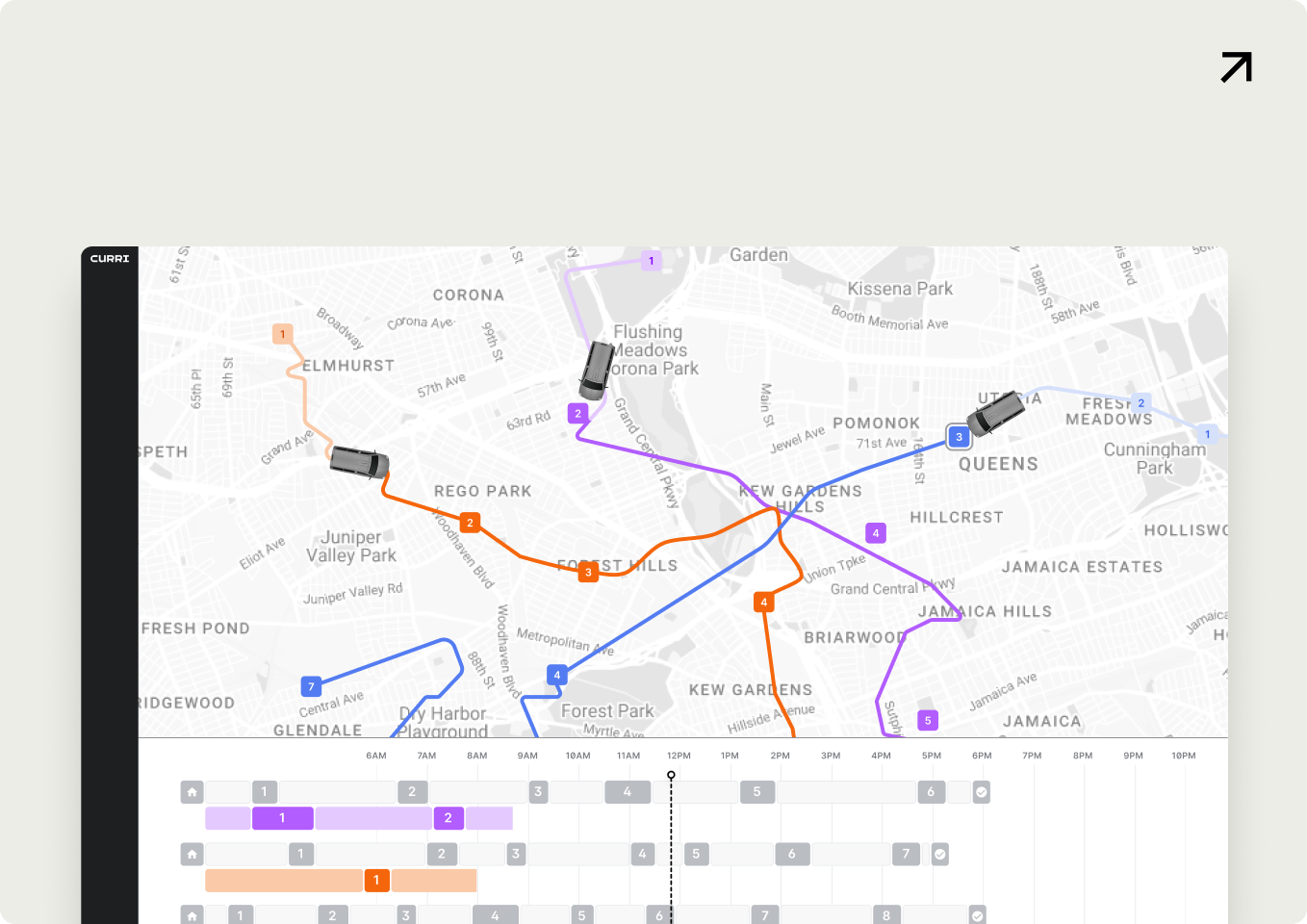
Intelligent Matching for Optimal Service Providers
Curri’s AI-powered platform has your back for supply chain exception management. It’s not just about getting deliveries from point A to point B—it’s about doing it smarter. We make last-minute LTL shipments hassle-free by providing an intuitive booking system that matches you with the right-size vehicle for your delivery with instant real-time pricing.
Our agents resolve exceptions on the fly, assist drivers in real-time, and make sure that you and your customers’ experience is world-class.
Best Practices for Managing Supply Chain Exceptions
Here are some tips to keep supply chain exceptions from throwing your business off track.
Standardize Exception Handling Procedures
It’s crucial to standardize how you handle these bumps in the road. Let’s break down some straightforward tips to help you stay on track.
- Use a central system to track and report exceptions. This way, the whole team can see what’s going on and where things stand.
- Regularly train your staff on how to spot and fix issues fast. The more they practice, the quicker they’ll react when something goes wrong.
- Keep a record of every exception and how it was resolved. Use these records for training and to improve your processes over time.
- If a truck is behind schedule, you should know immediately. Automated alerts give you the chance to address issues before they cause bigger delays on the job site.
- Make it easy for your drivers and logistics team to report potential problems before they become major issues.
Thank you for reading this article. Please enjoy $40 off any Curri delivery by clicking on this link to sign-up.
Use Advanced Analytics and Predictive Tools
Curri’s got your back when it comes to using advanced analytics and predictive tools. Curri uses AI to analyze data and predict what might go wrong - like delays or bottlenecks - to fix things before they become a headache.
With Curri, you don’t have to guess the best option for a delivery. Curri's AI ensures better resource allocation and optimal load planning. For example, our AI can identify when a hotshot is a better option than someone from your fleet who doesn’t have time for another delivery.
Also, you can easily monitor and analyze delivery metrics at a branch level, giving you clear insights into your last-mile performance and costs.
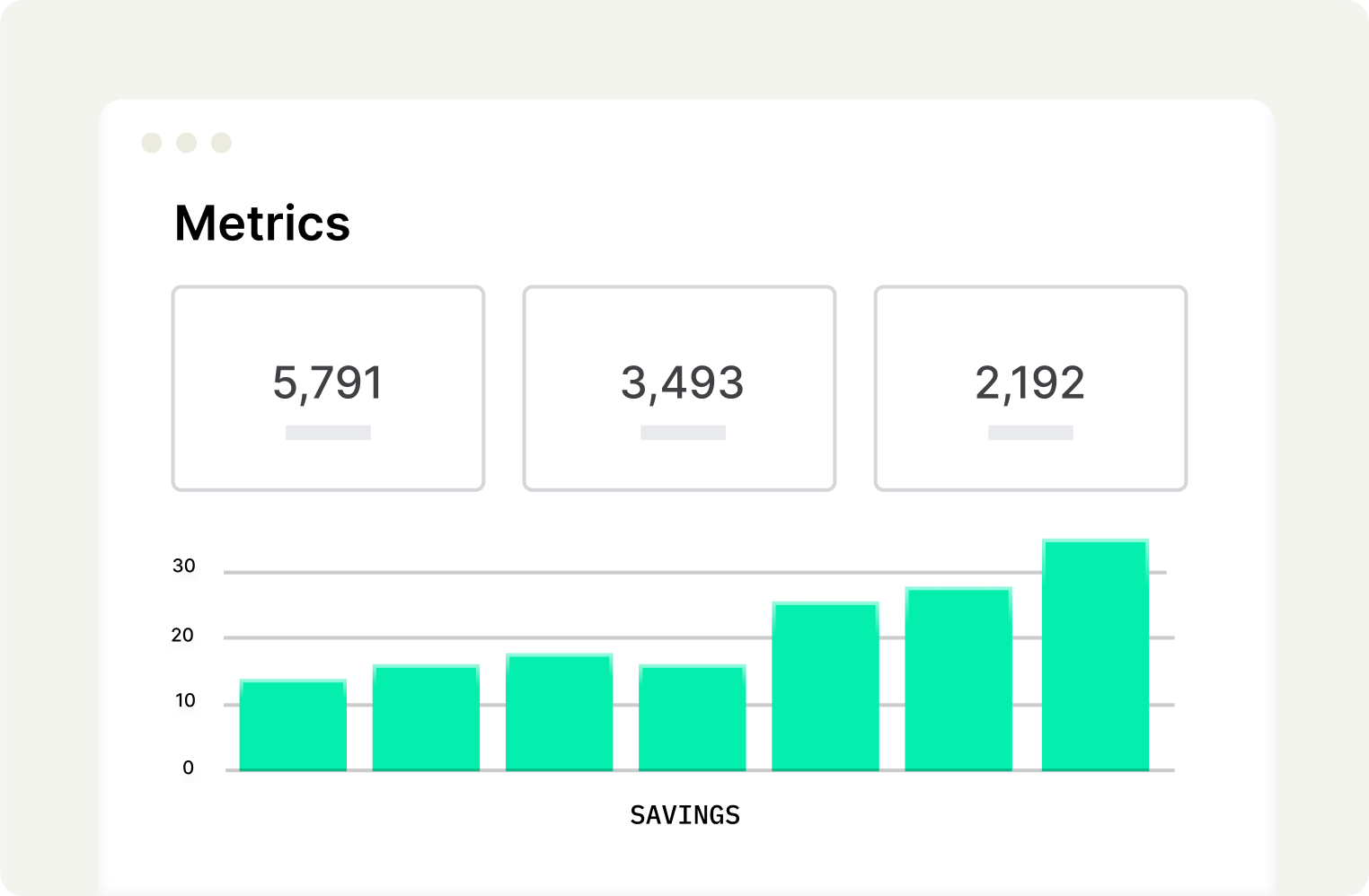
Collaborate with Reliable Suppliers and Partners
At Curri, every driver who joins our platform undergoes a series of background checks and verifications. This includes SAFER verifications and ensuring DOT-regulated carriers are in good standing with FMCSA regulations. We don’t cut corners because we know how important it is for you to trust the people handling your deliveries.
Curri also offers dedicated trucking services. This means you get a truck and driver exclusively for your business, often tailored to specific routes or needs. No more worrying about shared loads or mixed schedules.
Implement Real-Time Monitoring Systems
With real-time monitoring, you get instant updates. If a truck gets delayed or a route needs changing, you’ll know right away. This is important for supply chain exception management, because a system is only as good as the data it has.
Curri’s platform makes this easy. It gives you full visibility into your deliveries. Whether you’re tracking one truck or a whole fleet, you’ll see exactly where everything is. And that helps you manage your logistics better.
Conclusion
Instead of dreading supply chain exceptions, look at them as a way to strengthen your supply chain. Every challenge you solve adds a layer of resilience to your business. The better you manage these hiccups, the smoother everything else runs.
Curri makes handling supply chain exceptions easier than ever. Your customers deserve on-time delivery. We can help you do it every day. Get a Demo Curri or create a free account and see the difference for yourself.
Thank you for reading this article. Please enjoy $40 off any Curri delivery by clicking on this link to sign-up.
FAQs About Exception Management in Logistics
How long does a shipment exception last?
A shipment exception can last anywhere from a few hours to a few days, depending on the issue and how quickly it's resolved. The length of time can vary based on factors like the type of exception, the responsiveness of the carrier, and how quickly alternative arrangements can be made.
What is the difference between an exception and a delay in logistics?
An exception in logistics refers to any unexpected event that disrupts the normal delivery process, such as a wrong address, damaged goods, or a missed delivery attempt. A delay, on the other hand, is specifically when a shipment takes longer than expected to reach its destination.
What steps should be taken when a shipping exception occurs?
When an exception occurs, first, identify the issue and its cause. Then, communicate with all relevant parties, including the carrier and the customer, to keep everyone informed. Next, take corrective action, such as rerouting the shipment or rescheduling the delivery. Finally, document the exception and review the process to prevent similar issues in the future.